The pinion in gear, a fundamental component in the realm of mechanical engineering, plays a pivotal role in the transmission of power and motion within machinery. As a crucial element in gear systems, the pinion is essentially a small gear with a limited number of teeth, designed to mesh with a larger gear, known as the gear wheel or crown wheel, to achieve a specific gear ratio. This gear ratio is critical in modifying the speed and torque of the rotational motion, thereby allowing machines to operate efficiently across a wide range of applications, from automotive transmissions to industrial machinery.
Key Points
- The pinion in gear is a small gear with a limited number of teeth, crucial for achieving specific gear ratios in mechanical systems.
- Gear ratios are essential for modifying the speed and torque of rotational motion, enabling machines to operate efficiently across various applications.
- The design and material selection of pinions are critical factors influencing their performance, durability, and overall system efficiency.
- Precise manufacturing techniques and quality control measures are necessary to ensure the pinion's dimensional accuracy and surface finish, which directly impact the system's reliability and noise reduction.
- Understanding the principles of gear mechanics and the role of pinions is vital for the development, maintenance, and optimization of mechanical systems in diverse industries.
Design and Manufacturing Considerations
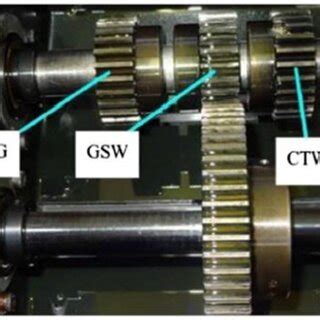
The design of a pinion in gear involves careful consideration of several factors, including the number of teeth, the pitch circle diameter, the addendum and dedendum, and the material from which it is made. The number of teeth on a pinion is a critical parameter, as it determines the gear ratio when meshed with a larger gear. A smaller number of teeth results in a higher gear ratio, which can be beneficial for increasing torque at the expense of speed. However, it also increases the likelihood of tooth breakage and reduces the system’s efficiency due to higher frictional losses.
The material selection for pinions is equally important, with common materials including steel, bronze, and plastics. Steel is often preferred for its high strength and durability, although it may require additional surface treatments to reduce friction and wear. Bronze and plastics, on the other hand, offer advantages in terms of corrosion resistance and noise reduction but may lack the necessary strength for high-torque applications. The manufacturing process for pinions involves precision machining techniques, such as hobbing, shaping, and grinding, to achieve the required dimensional accuracy and surface finish.
Performance and Efficiency
The performance and efficiency of a gear system are significantly influenced by the design and manufacturing quality of the pinion. A well-designed pinion with precise tooth profiles and a smooth surface finish can minimize frictional losses, reduce noise, and enhance the overall efficiency of the system. Conversely, a poorly designed or manufactured pinion can lead to premature wear, increased energy consumption, and reduced system reliability. Theoretical models, such as the Lewis equation, are used to predict the stress and fatigue life of gear teeth, helping engineers to optimize pinion design for specific applications.
Pinion Parameter | Typical Value Range |
---|---|
Number of Teeth | 10-100 |
Pitch Circle Diameter (mm) | 20-500 |
Material | Steel, Bronze, Plastics |
Surface Roughness (μm) | 0.1-1.6 |
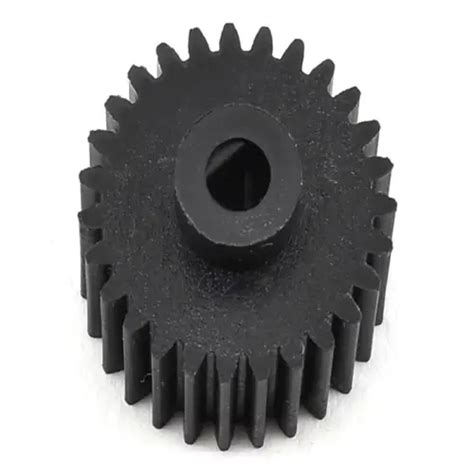
Applications and Future Directions
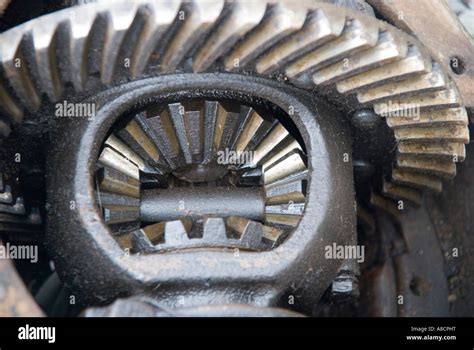
Pinion in gear systems are ubiquitous in modern machinery, finding applications in automotive transmissions, gearboxes for industrial machinery, and even in the mechanisms of watches and other precision instruments. The ongoing quest for efficiency, reliability, and compactness drives innovation in pinion design and manufacturing. Advances in materials science, such as the development of advanced composites and nanostructured materials, offer potential for improving the strength-to-weight ratio and reducing friction in gear systems. Additionally, the integration of smart materials and sensors into gear systems can enable real-time monitoring and adaptive control, further enhancing performance and efficiency.
The future of pinion in gear technology also involves the exploration of novel gear geometries and tooth profiles, designed to optimize specific performance criteria such as efficiency, noise reduction, or durability. Computational models and simulation tools play a crucial role in this process, allowing engineers to predict and optimize the behavior of complex gear systems under various operating conditions. As technology continues to evolve, the pinion in gear will remain a vital component in the machinery that underpins modern society, with its design and performance influencing the efficiency, reliability, and sustainability of a wide range of industrial and consumer products.
What is the primary function of a pinion in a gear system?
+The primary function of a pinion is to mesh with a larger gear to achieve a specific gear ratio, thereby modifying the speed and torque of the rotational motion.
How does the material selection for a pinion influence its performance?
+The material selection for a pinion influences its strength, durability, frictional characteristics, and resistance to corrosion. Common materials include steel for high strength, bronze for corrosion resistance, and plastics for noise reduction.
What factors contribute to the efficiency of a pinion in gear system?
+The efficiency of a pinion in gear system is influenced by the design of the tooth profiles, the surface finish, the material properties, and the lubrication strategy. A well-designed and manufactured pinion with appropriate lubrication can minimize frictional losses and maximize system efficiency.